I’ve had my K40 for over a year now. I’ve burned leather, engraved and cut wood and acrylic. I’ve made hundreds of things for gifts, decorations and even made custom commissioned items for friends. It’s been great.
But it’s been a struggle. Don’t get me wrong, the K40 is a great starter machine for this kind of work, but it seems to be pushing its limits for cutting acrylic. It takes a bit of effort to calibrate, align and focus the laser correctly for maximum efficiency, which is needed for acrylic work.
Because I’m running up a deadline for mass-producing an item (wings for the DC540 Chakra badge) and production wasn’t meeting requirements, I decided to invest in a larger machine. Being budget conscious, I chose the manual focus version of the Omtech 80W machine.
It arrived last week, and I’m going to try and encapsulate my experience/lessons learned over the past week in this post.
I was relieved that the crate arrived unharmed. As my wife suggested, I’ll probably cut out that lovely tagline for wall art at some point. 🙂
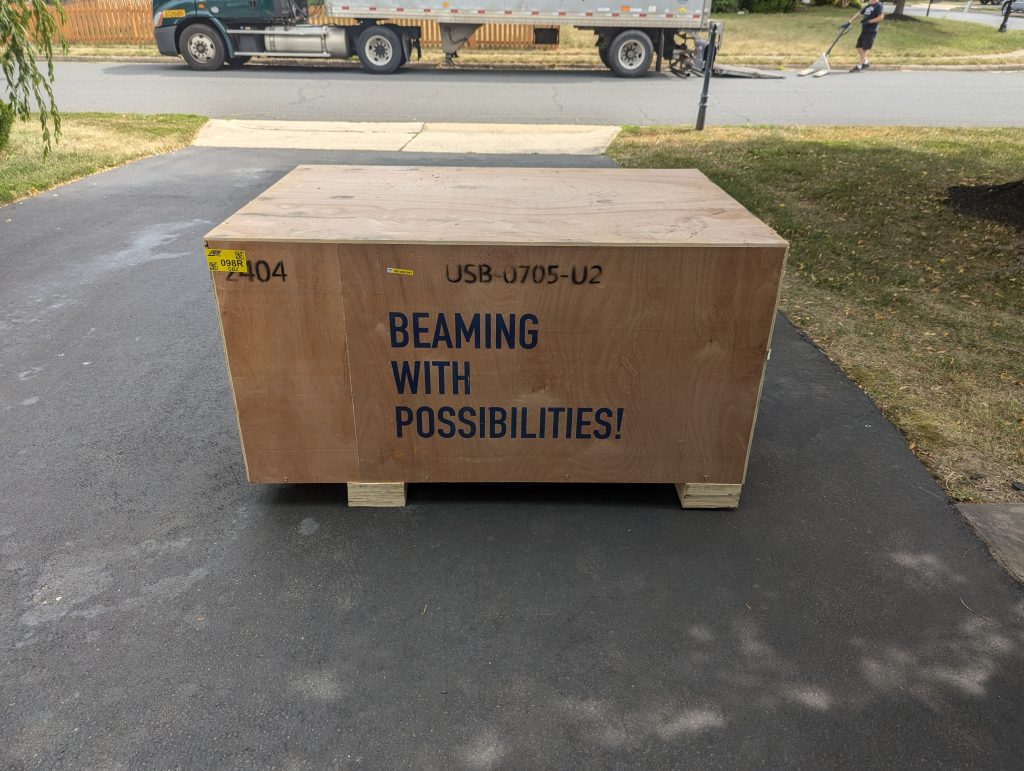
After a bit of work uncrating and positioning the 200+ lb unit in the garage, I went through the installation and testing process.
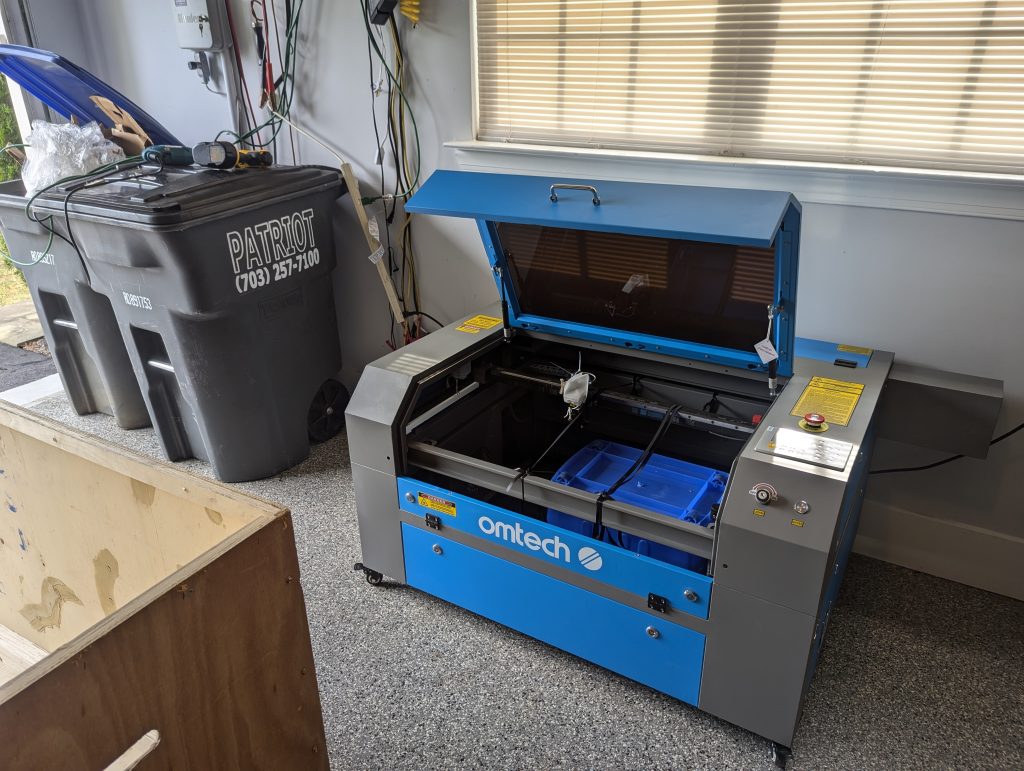
The first test cut demonstrated two things. First, I had the focus wrong. Second, this thing has way more power than a K40. When the K40 is out of focus, it barely penetrates acrylic. When this thing is out of focus, it just makes thicker lines and doesn’t make it all the way through.
The first major difference between the two units is the size. The K40 can be lifted and moved from room to room by one person of average strength. It’s a tabletop unit. Not so with the 80W. I waffled between the garage and the basement for this unit, for various reasons. Garage = easier installation, easier venting of exhaust. Basement, better climate control, better integration with the rest of the lab. I opted for the garage. Sometime before winter, I will enlist three strong friends to help bring it into the basement and reconfigure exhaust.
Next obvious difference is the bed. The K40 ships with a fixed bed. It’s actually bolted on extension poles from the bottom of the cabinet. No provision exists in the unit to adjust the bed height. This is problematic. I ended up buying a lab jack and removing the extension poles. And cheap lab jacks are inherently not level. Oh well. I worked around it, but it was troubleshom. The 80W unit comes with linked greased screw adjusters for the entire bed, controllable by a single knob.
The K40 has no focus assistance at all. Trial and error (weighted heavily on the side of error) is used to find the correct focal point for your material. The 80W includes a red-dot focus tool. I simply turned the bed level adjustment knob until the red dot was at its smallest, and bam, I had good focus. The red dot is a little bit off in the X/Y coordinates from where the beam hits, but that’s easily adjustable as well (critical if you’re using the red dot to validate framing before cutting/engraving).
The mirror mounts on the K40 are not great. On mine, they look kind of like this, but the mirror is much closer to the surrounding ring than this photo. The result is that when you use tape as recommended to calibrate and center the beam on each mirror, invariable there ends up a bit of tape or burn residue on the mirror.
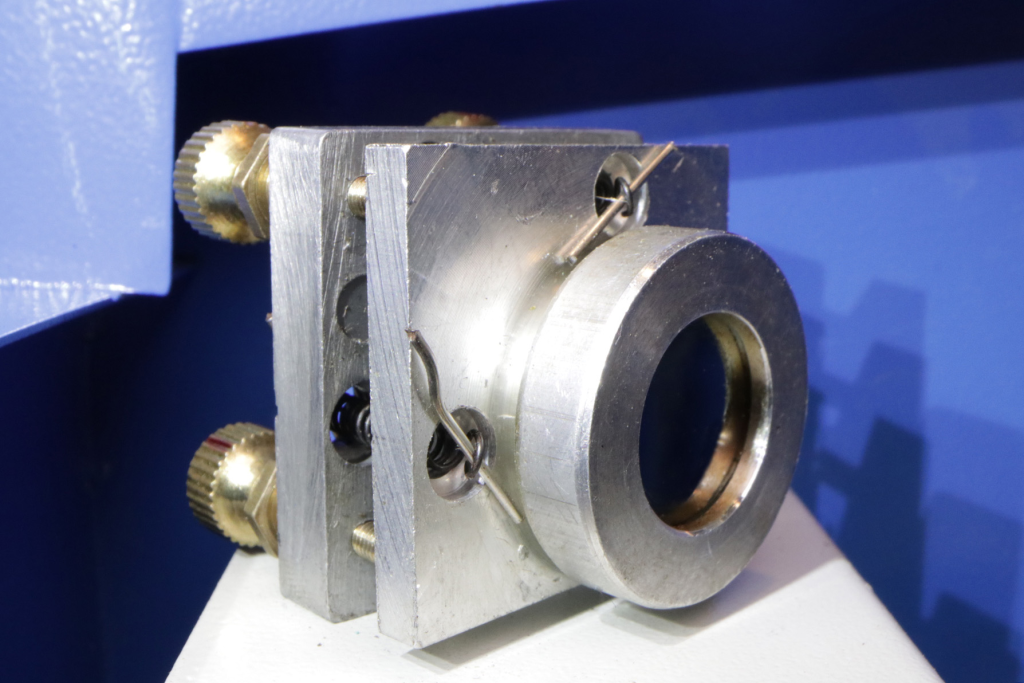
The new unit includes an offset frame for exactly that purpose. It’s not close to the mirror, so there’s no risk of tarnishing the mirror, yet it’s still aligned with the mount, so you can trust the alignment by putting tape on that frame and pulsing the laser.

The K40 has very little in the way of controls. A simple power level display, up/down buttons, an emergency stop button, and a pulse button. This unit has a full display which shows a representation of the pattern being cut/engraved, including a real-time cursor of what’s being cut.
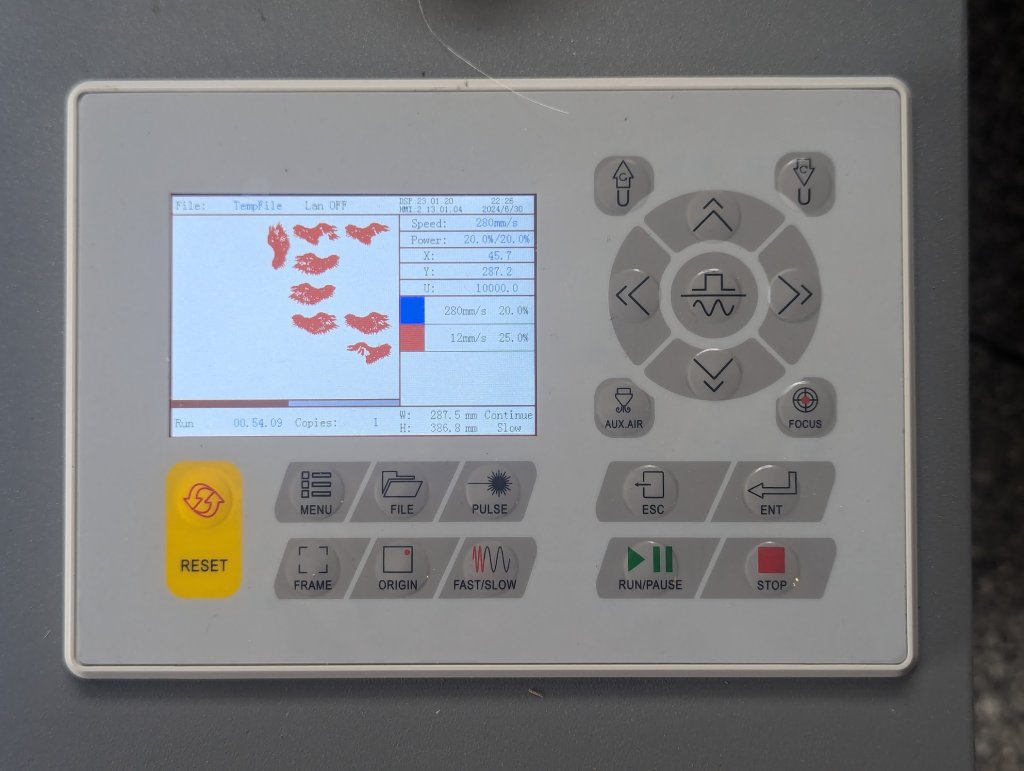
My K40 would have required a controller upgrade to work with Lightburn — therefore I would have to set the power level on the panel, and use K40 Whisperer to send the operation code to the unit.
It was trivial to attach this unit to my PC using Lightburn, and since I already had a Lightburn license for my diode laser, I just had to add a DSP license to control the OMTech unit. Lightburn is miles beyond K40 Whisperer in functionality, including dragging, rotating, duplicating and removing design elements to suit your material before starting the job. Plus it’s easy to control design elements by color, assigning each color to line, fill or offset fill as desired.
Something I learned during this process, relating to my specific use case, is about vector vs raster. Most of what I do is engraving acrylic to foster illumination of patterns in acrylic. With the K40, vector engraving was fine for main design lines. With the new unit, the focal point is much smaller. Maybe that is an indication that the K40 was never completely dialed in on a good focal point, or maybe the beam and lens combination is just that much better on the 80W unit, but the end result is that I can no longer use vector lines for main lines of illumination. They’re fine for fine details and accents, but the big lines are going to need raster from now on. Raster takes a bit longer to cut, but that’s fine.
By the way, if you’re considering this unit or one like it, consider laser cooling solutions. It comes with a water pump, but from experience, I’ll tell you that the stock water pumps on these things are perilously unreliable, and if the pump fails you will lose your tube. Consider an industrial chiller. I ended up buying a CW3000 for the K40. It’s not a true chiller, more of an enhanced water pump, but the enhancements include alarms and alarm outputs for sensing flow failure or high temperatures. Since the new unit is in the garage, and the garage gets hot in the sweltering Virginia summer, I opted for a true chiller with compressor (CW5200) for this unit. Same safety features, but it actually cools the water. The last thing I want to do is replace a blown tube on this unit.
I wish I had upgraded to this unit earlier, but the K40 was a great training ground for CO2 laser work.